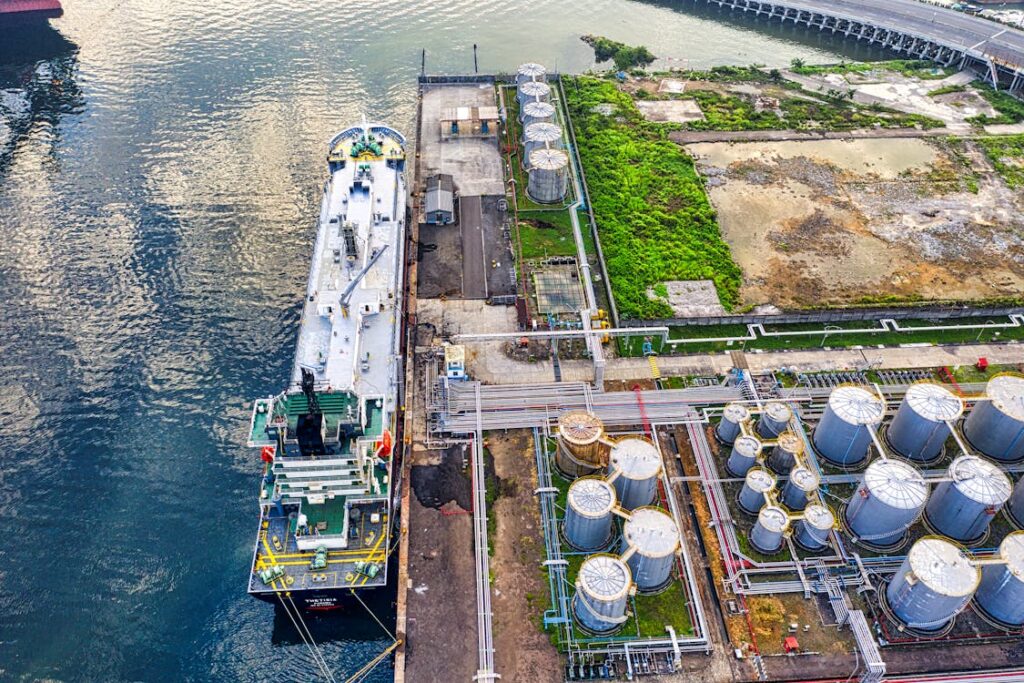
Above-ground storage tanks (ASTs) are critical assets in industries such as oil and gas, enabling the storage of essential resources like crude oil and refined products. These tanks are governed by stringent standards like API 653, which dictate inspection intervals and maintenance requirements. While these regulations ensure safety and compliance, they also present challenges—outages lasting six months or more, ballooning costs, and inconsistent execution. In today’s fast-paced industry, optimizing AST outages has become a necessity for staying competitive.
Traditionally, AST maintenance programs relied on decentralized, reactive approaches that were costly and inefficient. Each project was treated as a standalone effort, with contractors often holding the upper hand in determining costs and timelines. This model led to excessive expenses, weak accountability, and misalignment among teams. By shifting to a centralized and proactive strategy, organizations can transform AST management into a streamlined, cost-effective operation that achieves both compliance and business goals.
The cornerstone of effective AST optimization is risk-based planning. Rather than defaulting to fixed inspection intervals, organizations can evaluate each tank’s risk level and prioritize maintenance accordingly. High-risk tanks are addressed immediately, while inspections for low-risk tanks are grouped strategically to reduce downtime and costs. By incorporating long-term forecasting and predictive analytics, teams can develop a comprehensive maintenance schedule that anticipates needs years in advance.
One of the most significant challenges in AST maintenance is the prolonged duration of outages. Cleaning, inspection, and coating processes often extend for months, keeping valuable tanks out of service. Optimization efforts focus on identifying and addressing inefficiencies within these processes. For instance, streamlining sludge removal methods and reducing gaps between vendor transitions can compress outage timelines significantly. These improvements not only save time but also minimize revenue loss, allowing organizations to get their tanks back online faster.
Contractor management is another critical area of improvement. In the past, contractors operated with minimal oversight, often dictating costs and schedules. A more structured approach involves defining clear scopes of work, implementing standardized pay structures, and tracking performance through data-driven tools. By renegotiating contracts based on actual performance metrics, organizations can regain control and align contractor efforts with project objectives.
Data plays a transformative role in AST outage optimization. Field data capture tools provide real-time insights into performance, enabling teams to identify bottlenecks and inefficiencies. Over time, this data becomes the foundation for predictive modeling, allowing for smarter planning and execution. A “plan, do, check, act” model ensures continuous improvement, with lessons learned from each project informing future initiatives.
Cultural transformation is equally essential. Teams must shift from a reactive mindset to a proactive, performance-driven approach. Empowering managers with real-time data and transparent tools enables them to make informed decisions and foster collaboration among contractors and stakeholders. For example, daily planning tools that highlight variances between planned and actual progress can encourage contractors to align their efforts with organizational goals, creating a more cooperative environment.
The results of AST optimization speak for themselves. Organizations that embrace this approach have achieved reductions of up to 34% in execution costs, 37% in oil loss, and 33% in outage durations. Beyond these tangible benefits, optimized AST programs ensure compliance, build resilience, and set a foundation for sustainable, long-term asset management. With the right strategy, tools, and cultural commitment, AST optimization becomes more than a maintenance strategy—it becomes a competitive advantage that drives efficiency and success.